Call us now:
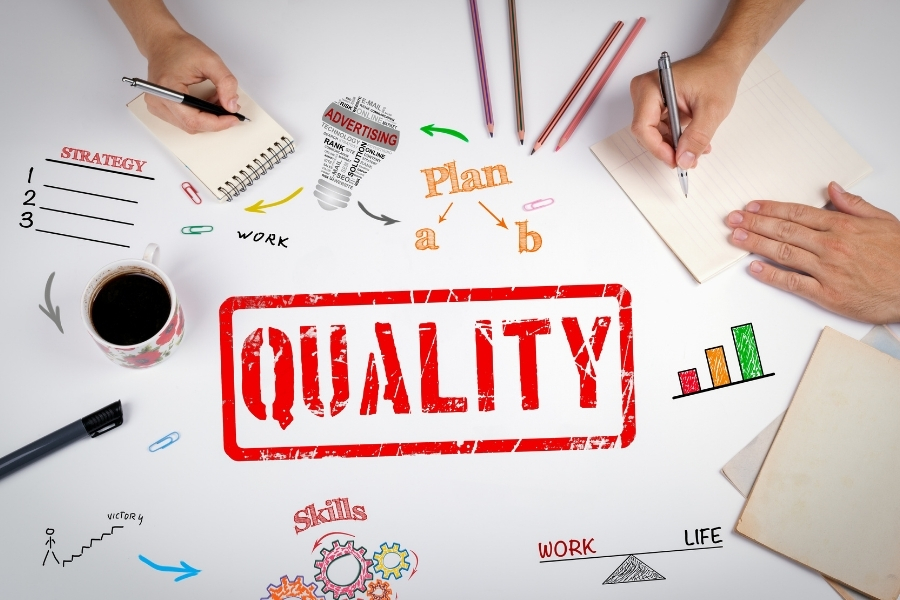
5 Common Textile Quality Mistakes — and How to Avoid Them
In the fast-paced textile industry, where quality and compliance drive customer satisfaction and brand loyalty, even a small lapse can lead to costly consequences. Whether you’re manufacturing for global brands or domestic retailers, maintaining consistent quality across production stages is non-negotiable. Yet, many factories and vendors continue to face recurring issues that could be easily avoided with the right systems in place.
1. Skipping Pre-Production Meetings
The Mistake:
Rushing into production without clearly aligning on specifications, timelines, and quality checkpoints often leads to miscommunication and errors down the line.
How to Avoid It:
Always conduct a structured pre-production meeting involving QA, merchandising, and production teams. Review all technical packs, samples, and buyer expectations in detail before greenlighting bulk production.
2. Inadequate Fabric Inspection
The Mistake:
Failing to inspect raw fabric or accepting rolls with hidden defects can result in large-scale wastage and delayed deliveries.
How to Avoid It:
Implement a systematic 4-point fabric inspection method. Ensure that only fabric passing quality standards is accepted and recorded with traceable documentation.
3. Irregular Inline Inspections
The Mistake:
If you’re only checking quality at the end of production, it’s already too late. Defects detected post-production mean higher rework and rejection rates.
How to Avoid It:
Schedule regular inline inspections at each stage — stitching, finishing, packing. Real-time monitoring enables immediate corrective actions, drastically reducing rework.
4. No Corrective and Preventive Action (CAPA) Plan
The Mistake:
Recurring issues are often ignored or handled temporarily without a root cause analysis, leading to quality inconsistencies.
How to Avoid It:
Create a CAPA system where each defect triggers an investigation, solution, and follow-up. Close all CAPAs within a set timeline (e.g., 15 days) and train the team on updated practices.
5. Undertrained QA Teams
The Mistake:
QA teams lacking up-to-date knowledge on standards, buyer requirements, and SOPs are prone to miss critical quality parameters.
How to Avoid It:
Invest in monthly QA training, on-the-job coaching, and performance reviews. Empower your QA personnel with tools, checklists, and data to enforce quality at every touchpoint.